China Manufacturer for Alcohol Making Machine - Double Mash column three-effect differential pressure distillation process – Jinta
China Manufacturer for Alcohol Making Machine - Double Mash column three-effect differential pressure distillation process – Jinta Detail:
Overview
The double-column distillation production of the general-grade alcohol process mainly consists of the fine tower II, the coarse tower II, the refined tower I, and the coarse tower I. One system contains two coarse towers, two fine towers, and one tower enters the steam four towers. The differential pressure between the tower and the tower and the temperature difference are used to gradually exchange heat through the reboiler to achieve the purpose of energy saving. In the work, the two crude towers are fed simultaneously, and the two fine towers simultaneously take alcohol. At present, the process has been promoted in many general-grade alcohol and fuel ethanol manufacturers.
Third, the process characteristics
1. Low energy consumption, 1.2 tons of alcohol consumption.
2. One steam passes through the reboiler to heat the fine tower II, the fine tower II top wine vapor heats the crude tower II through the reboiler, the crude tower II top wine vapor directly heats the fine tower I, and the fine tower I tower top wine passes through The reboiler heats the crude column I. One tower enters the steam and four towers to achieve three-effect thermal coupling to achieve energy saving.
3. Using the differential pressure and temperature difference between the tower and the tower to gradually exchange heat through the reboiler, the heat can be utilized to the maximum extent, thereby effectively saving energy.
Fourth, the process
Five, heating method
The key to the energy saving of the process is the heating mode. The primary steam is indirectly heated by the reboiler to clean the tower II. The steam condensed water preheats the mature fermentation mash and the crude alcohol and then returns to the boiler soft water tank for reuse; the refined tower II wine vapor passes through the reboiler. The crude column II is heated; the fine column I wine vapor is heated by the reboiler to the crude column I.
In this process, the crude tower I is a negative pressure tower, the coarse tower II and the fine tower I are atmospheric pressure towers, and the fine tower II is a positive pressure tower. The pressure difference and the temperature difference are used for stepwise heating. One tower enters the steam and three towers to achieve three-effect thermal coupling to achieve energy-saving purposes.
Sixth, the material trend
The two-stage preheated fermentation mash first enters the top of the crude column I to remove the aldehyde, and then divides the mash into two parts through the distributor: one part enters the coarse column II, and the other part enters the coarse column I. After the fermented mash enters the crude tower II, the bad liquid is removed from the bottom of the tower, and the crude liquor enters the fine tower I to be concentrated and discharged, and part of the finished alcohol is taken out at the upper side line.
After the bottom of the refined tower I light wine and the crude tower I top wine vapor condensate, it enters the fine tower II, concentrates and removes in the fine tower II, and takes out some of the finished alcohol in the upper side line, and the high boiling point impurities such as fusel oil Take out from the lower part of the fine tower II.
Seven, the general level of alcohol consumption and quality comparison table
Product detail pictures:
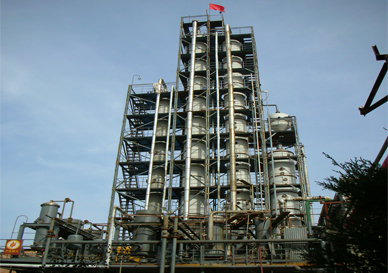
Related Product Guide:
Just about every member from our large efficiency income crew values customers' wants and enterprise communication for China Manufacturer for Alcohol Making Machine - Double Mash column three-effect differential pressure distillation process – Jinta , The product will supply to all over the world, such as: Cancun, Algeria, Macedonia, Based on our automatic production line, steady material purchase channel and quick subcontract systems have been built in mainland China to meet customer's wider and higher requirement in recent years. We are looking forward to cooperating with more clients worldwide for common development and mutual benefit!Your trust and approval are the best reward for our efforts. Keeping honest, innovative and efficient, we sincerely expect that we can be business partners to create our brilliant future!

The accounts manager made a detailed introduction about the product, so that we have a comprehensive understanding of the product, and ultimately we decided to cooperate.
